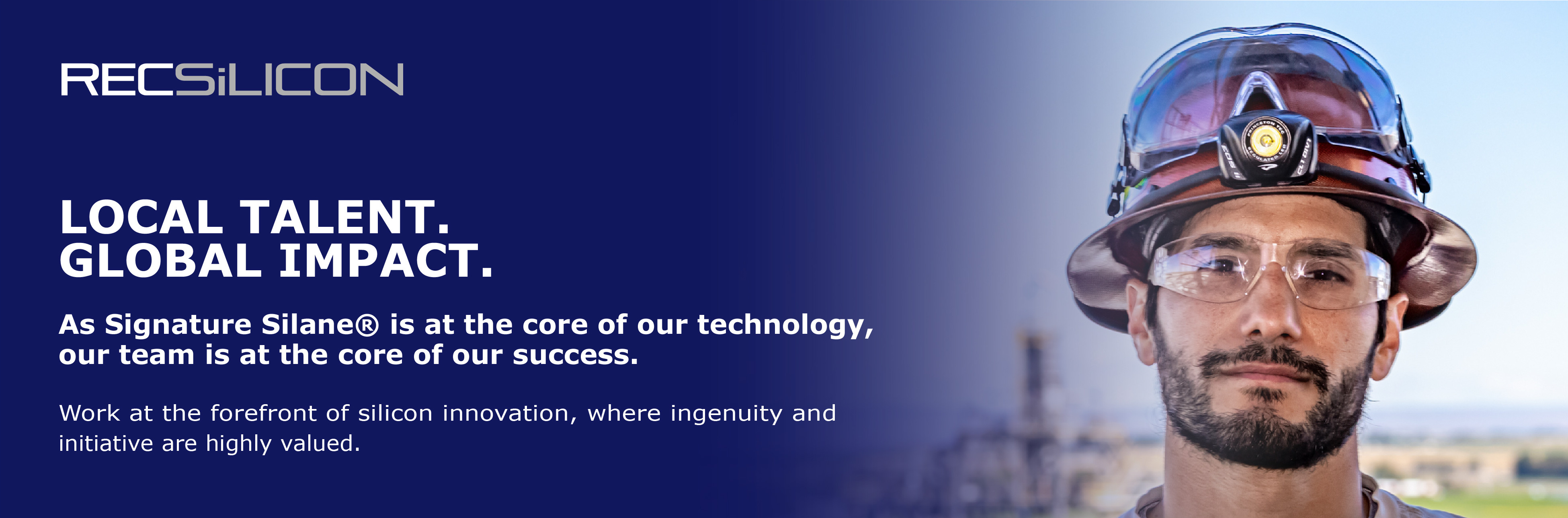
Position Description
REC Silicon is committed to the holistic approach with our company benefits. Once you’re here, you’re family and we want you to be safe, healthy, and engaged during your rewarding career. Designed not just for our team, but also families, our benefits offer the following:
- Generous PTO: Your off time is important. We offer 144 hours of PTO per year for the first 5 years of employment. Year six, 184 hours. High maximum balance and cash out option.
- Medical/Dental/Vision: Majority of premiums paid by REC Silicon for you and your dependents. Includes virtual medical and mental health options.
- Additional Health Coverage: FSA and HSA available. Voluntary insurance options include life and AD&D, accident, hospitalization and critical illness.
- Earn More: We offer a generous annual company bonus plan in addition to salary/wage.
- 401(k) Savings Plan: Jump start your retirement with REC Silicon’s discretionary contribution that increases with longevity and does not require an employee contribution. Match also available.
- Company-Paid Benefits: Life insurance, short & long-term disability insurance, Life Flight, Employee Assistance Program (EAP), wellness reward program, pharmacy advocacy and disease management program.
- Flexibility: We support employees through flexible work schedules and limited work from home options.
- Additional Benefits: We provide position-based clothing, travel expenses, training and additional materials needed on a case-by-case basis.
Salary Range
$87,440 - $131,160 / year
The API (510, 570) Inspector position is considered safety sensitive work and if a job offer is accepted the applicant will be required to complete pre-employment drug and alcohol testing which will include cannabis testing.
Summary
Responsible to ensure that the requirements of American Petroleum Institute (API) 510 and 570 and the National Board Inspection Code (NBIC) on inspection, examination, and testing are met, and shall be directly involved with the infield inspection activities. Also, responsible for overseeing site specific Inspection Quality program on behalf of REC Silicon.
Essential Duties and Responsibilities
The following examples of duties and responsibilities illustrate the general range of tasks assigned to the position but are not intended to define the limits of required duties. Other essential duties may be assigned consistent with the general scope of the position.
- Perform internal and external inspections to determine if a weldment of equipment meets the acceptance criteria of a specific code, standard or document
- Schedule and coordinate inspections on equipment at scheduled intervals to maintain the mechanical integrity of the fixed equipment of the facility
- Review and approve reports, findings, and conclusions of NDE examinations
- Determine and schedule path forward activities to address in field test results in compliance with API standards
- Submit Reports of Inspections to the Chief Inspector and all other required reports in the prescribed timeline
- Recommend and approve repairs as well as performing visual inspection of completed work
- Evaluate inspection results and update plans, service life, and operating conditions to ensure condition of fixed equipment is known to ensure safe operations
- Maintain up to date knowledge on equipment leak regulations applicable to location and customer base
- Cooperate with personnel of the Maintenance and Engineering Department on problems of scheduling, methods of repair, materials utilization and in arranging special inspection and advice on inspection requirements, corrosion allowances, access provisions, etc. for new designs
- Request the services of the Materials Scientist and the Reliability Engineer for Fixed Equipment on critical and unusual problems involving the cause, seriousness and prevention of corrosion or other deterioration of plant equipment and on development of inspection methods
- Serve as the authorized piping inspector for determining that the requirements of API 570 on inspection, examination and testing are met
- Ensure that personnel performing non-destructive examinations adhere to relevant Codes and Recommended Practices as defined in API 510 and 570
Qualifications
Incumbents must have demonstrated knowledge and abilities in these areas. The requirements listed below are representative of the knowledge, skill, and/or ability required.
Education and/or Experience
- Requires HS Diploma or equivalent and three (3) years of experience in weld inspection related activities (for example, QC, NDE); or equivalent combination of educations and experience
- Requires an extensive knowledge of industry standards including NBIC, AWS, ASME, API (510 & 570) and demonstrated working knowledge of Non-Destructive Examiner methodologies
- Must have the ability to obtain certification of API 510 within 6 months (Vessels)
- Must have the ability to obtain certification of API 570 within 6 months (Piping)
- Must have the ability to obtain NBIC certification
- Must have the ability to obtain Certification for Special Inspector by State of Washington Department of Labor and Industries (L&I) Boilers and Pressure Vessels (BPV) program (Washington State employees only)
Computer Skills
- Basic knowledge of computers, including Microsoft Word, Excel and Outlook and ability to learn new computer programs
Other Skills and Abilities
- Must have the ability to properly interpret regulations, codes, and industry standards
- Strong attention to detail
These skills and abilities are typically acquired through a combination of education, experience, and training. This combination will provide the competence to perform the work of the position.
Environmental Responsibilities
REC is committed to managing its manufacturing operations in a manner that is environmentally responsible and protects the current and future environmental interests of all interested parties within which the company operates. It is each employee’s responsibility to recognize and report environmental concerns to appropriate management and HSE staff.
Supervisory and Budgetary Responsibilities
- None
Physical Demands
The physical demands described here are representative of those that must be met by an employee to successfully perform the essential functions of this job.
- While performing the duties of this job, the employee is regularly required to use hands to finger, handle, or feel; reach with hands and arms; climb or balance and talk or hear
- The employee frequently is required to stand; walk; sit; stoop, kneel, crouch, or crawl; and taste or smell
- The employee must frequently lift and/or move up to 25 pounds and occasionally push and/or move up to 100 pounds
- Specific vision abilities required by this job include close vision, distance vision, color vision, peripheral vision, depth perception, and ability to adjust focus
Work Environment
The work environment characteristics described here are representative of those an employee encounters while performing the essential functions of this job. Reasonable accommodations may be made to enable individuals with disabilities to perform the essential functions.
- While performing the duties of this job, the employee is frequently exposed to moving mechanical parts; high, precarious places; and outside weather conditions
- The temperatures range seasonally from below 0 degrees to 100 degrees out of doors
- The employee is occasionally exposed to fumes or airborne particles, toxic or caustic chemicals, risk of electrical shock, and risk of radiation
- The noise level in the work environment is usually loud
- Radio communication is required
- Hand trucks, dollies and forklifts are used to perform the job
- Ladders and stairs are climbed frequently